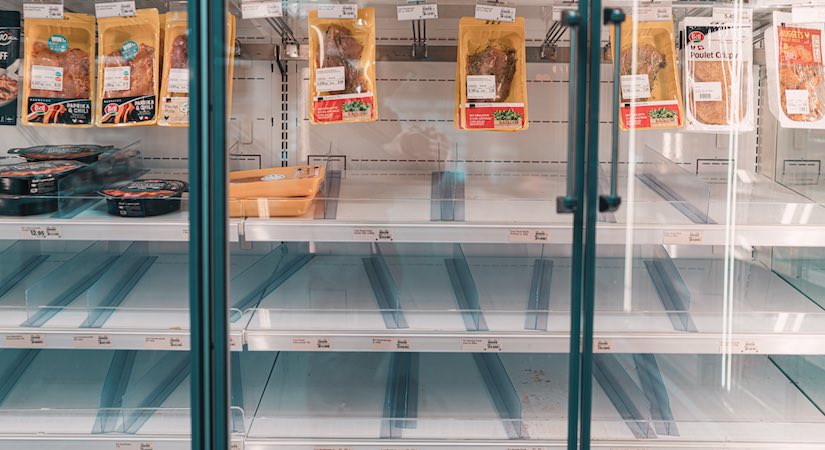
Tarnekindlus (või teenustase) on sedavõrd oluline näitaja, et lausa 83% Euroopa tuntud kaubamärkidest jälgib seda oma varustajate kvaliteedinäitajana. Ja pea pooled neist rakendavad trahve, kui teenustaseme täitmine ei vasta kokkulepitule1.
Kui jaekaubandusettevõtted asuvad üldjuhul väärtusahela lõpus, siis kaupu tootvad ettevõtted on omakorda kahe tule vahel. Ühest küljest survestavad neid tarneaegadega jaemüüjad ja samal ajal vaevlevad ise tooraine või allhankedetailide pakkujate kehva protsessilise soorituse käes.
Näiteks autotööstustele hüdraulikasüsteeme valmistav ettevõte Power-Packer Europa B.V. avastas, et 31.5% nende tarnekindluse probleemidest olid põhjustatud tootmiseks vajalike materjalide puudusest, kus 75 erinevat artiklit ei olnud lihtsalt õigeaegselt kohale jõudnud2.
Et oma partnerite kehva tarnekindluse sooritust kompenseerida, oli Power-Packer sunnitud oma materjalide baasvaru teatud gruppide lõikes rahaliselt suurendama lausa 53-84%.
Järelikult erinevate edukate ettevõtete suur tähelepanu tarnekindlusele ei ole asjata.
Mis on tarnekindlus?
Eelnevalt tuli välja, et tarnekindluse tähendus võib paista erinevatele osapooltele isemoodi. Mõnede ettevõtete jaoks tähendab see materjalide kättesaamist oma tarnijate käest, et õigeaegselt alustada tootmist või koosteprotsessi. Teiste jaoks omakorda on termin seotud toodete pakkumissuutlikkusega (tarnevõimega) lõpptarbijatele.
Mõlemal juhul tähendab tarnekindlus tõenäosust, et nõutud hulk tooteid jõuab soovijate kätte hetkel, kui nad seda vajavad ja mõõdetakse üldjuhul osakaaluna (või protsendina).
Tarnekindlus tähendab tõenäosust, et nõutud hulk tooteid satub soovijate kätte hetkel, kui nad seda vajavad.
Näiteks make-to-order (tellimispõhise) tootmise korral tähendab tarnekindlus täpsust, ehk tellimuste osakaalu, mis täideti tähtajaks või enne seda. Ehk siis osakaal tellimustest, mille läbimisaeg süsteemis oli väiksem, kui kliendile lubatud tarneaeg.
Läbimisaeg on aeg, mis kulub tootel tellimuse tekkimisest kuni selle jõudmiseni kliendini. Tarneaeg on omakorda juhtkonna (või ka näiteks jaekaubandusettevõtte) poolt seatud konstant. Järelikult sellest, kuidas tarneaeg on seatud, sõltub suuresti ka tarnekindlus.
Kui pakkuv ettevõte saab tarneaega ise määrata, võiks ta uhkustada väga kõrge tarnekindlusega. Kui see aga kujundatakse turu poolt, siis on tegemist juba konkurentsivõimet mõjutava teguriga.
Tarnekindla tarneaja arvutamine
Oletame, et klient soovib teha meiega lepingu konkreetsete koostude tootmiseks. Ta on nõus käed lööma vaid juhul, kui 95% tarnekindluse juures suudame neid tarnida 10 päeva jooksul. Kuna koostud on üsna kallid ja nõudlus juhuslik, siis tootmine toimub tellimispõhiselt.
Müügijuht, kes teab, et ühe sellise koostu tegemiseks kulub keskmiselt 8 päeva, on üsna kindel uue diili õnnestumises ja loeb mõtteis juba rahanumbreid. Tootmisjuht on aga üsna murelik. Miks?
Tal on põhjust muretsemiseks, sest 8 päeva on kõigest keskmine aeg ja müügijuht ei tea, et läbimisaja standardhälve on tegelikult 3 päeva. Nii suure variatsiooniga on nad 95% usaldusega võimelised pakkuma vaid 13-päevast tarneaega (täpsemalt 12,935).
Kui juhtkond soovib hankega edasi minna, siis peab tootmisjuht hakkama protsesse täiustama, et vähendada läbimisaega ja selle ajalist variatsiooni. Viimasel juhul saab abiks olla ka ostujuht, kes peaks nõudma oma partneritelt suuremat tarnetäpsust või lihtsalt praakima kehvemad pakkujad välja.
Tarnekindlus ja variatsioon
Nüüd võtame näiteks, et ostujuhil tuleb teha valik kahe ettevõtte vahel, kes mõlemad pakuvad sama koostedetaili. Seda tellitakse vaid vastavalt tootmisplaanis tekkinud vajadusele. Minimeerimaks võimalikke tõrkeid detailide puudumises, otsustatakse lisada tellimisajale väike turvapuhver.
Tulemuseks peaks olema olukord, kus detailid saabuvad kohale pisut enne nende tootmisse minekut ja ootavad seni toorainelaos. Meid huvitab eelkõige küsimus, kui suur peaks tellimise ajapuhver olema ja millise tarnijaga oleks see kõige optimaalsem?
Otsustamise teeb pealtäha keeruliseks olukord, et kummagi pakkuja keskmine tarneaeg on 10 päeva. Samas näitavad andmed, et Ettevõte 2 tarneajad on palju suurema variatsiooniga (võimalik, et nende nende protsessid ja kvaliteet pole kuigi head), kui seda on Ettevõtte 1 omad (vaata diagrammi all).
Et detailid oleks suure tõenäosusega tootmise hetkeks kohal, siis 95% tarnekindlusega võimaldab väiksem variatsioon Ettevõtte 1 korral rakendada 14-päevast tellimisaega, samas kui Ettevõtte 2 juhul oleks see lausa 23 päeva.
Nagu näha, siis Ettevõtte 2 korral on vaja tunduvalt suuremat ajapuhvrit selleks, et katta tarneaegade suurt variatiivsust.
Ühtlasi tasub märkida, et keskmine tellimus ootab Ettevõtte 1 tarnitud detailide korral laos 14 – 10 = 4 päeva, samal ajal kui Ettevõtte 2 saadetud detailid koguni 23 – 10 = 13 päeva. See on ajalises võrdluses 225% rohkem.
Järelikult tuleks ostujuhil valida koostööpartneriks suure ülekaaluga Ettevõte 1.
Tarnekindlus ja koosteprotsessid
Tarneaegade variatiivsus osutub selle kindluse seisukohast veelgi olulisemaks teguriks, kui tegemist on koostetootmisega, kus materjalide näol oodatakse sisendit mitmelt pakkujalt. Vältimaks igasugu viivitusi ja plaanimuudatusi, peavad detailid erinevatelt osapooltelt koosteprotsessi jõudma õigeaegselt. Sellest tulenevalt peab ka tarneaeg olema suurema varuga, kui see on näiteks ühe toote puhul.
Võtame näiteks olukorra, kus toote tegemiseks vajame komponente kokku kaheksast ettevõttest, kellede keskmised tarneajad ja variatsioonid on sarnased (näite arvutuste lihtsuse huvides). Järelikult saame rakendada ka kõigile sarnast turvalist tellimisaega.
Oletame, et kasutame siin sarnast tarnekindluse määra, kui eespool kahe tarnija võrdluses, mis tähendab, et ühe detaili vaates on sel 95% tõenäosus saabuda koosteprotsessi õigeks ajaks. Aga see veel ei tähenda, et kõikide detailide koondvaates oleks õigeks hetkeks saabumise tõenäosus sama suur. Vaid see on oluliselt väiksem nagu näitab allolev arvutus.
Tootmise koosteprotsess on võimeline õigeaegselt alustama vaid 66% juhtudest. Järelikult vajab ettevõte oluliselt pikemaid turvalisi tellimisaegu ja kõrgemaid tarnekindluse määrasid, et saavutada kõikide detailide koondina õigeaegne saabumine soovitud 95% tõenäosusega.
Selleks, et kõik 8 detaili, mida igaüht tarnib erinev ettevõte, oleks õigeaegselt kohal 95% juhtudest, peaks nende tarnekindlus eraldiseisvatena olema enam kui 99% nagu näitab allolev arvutus.
Kui tulla nüüd korraks tagasi jälle ühe komponendi juurde, siis eelnevalt nägime, et Ettevõtte 1 korral oli vaja 95% tarnekindluse juures 14-päevast turvalist tellimisaega. 99,36% tarnekindluse saavutamise juures kujuneks tellimisaeg aga juba 16 päeva pikkuseks. Järelikult tuleks ühel detailil keskmiselt laos seista 6 päeva.
Ettevõtte 2 korral oleks turvaline tellimisaeg pea kaks korda pikem, napilt alla 30 päeva (siinkohal tuletan meelde, et keskmine tarneaeg oli mõlemal ettevõttel sama), mistõttu tuleks ka ühel detailil laos viibida keskmiselt 20 päeva.
Kaheksa erineva komponendi korral oleks Ettevõtte 1 ja Ettevõte 2 sarnaste tarnijate võrdluses turvalise tellimisaja vahe 14 päeva. Siit saame järeldada, et stabiilsed tarnijad on tootmisettevõtte jaoks minimaalsete laovarude tõrgeteta tootmisplaani seisukohalt üliolulised, iseäranis veel olukorras, kus on tegu koosteprotsessidega.
Sama kehtib ka jaekaubandusettevõtete kohta. Stabiilsed tarnijad aitavad neil vähendada laovaru ja OOS (out-of-stock) olukordade tekkimisvõimalust.
Tarnekindlusest ja laovarude suurusest võid lugeda veel täiendavalt siit: “Laovarude vähendamise võimalikud strateegiad COVID-19 kriisiolukorraks“.
Tarnekindluse juhtimine
Nägime, et mitme komponendi tõenäosus õigeks ajaks kohale jõuda on seda väiksem, mida rohkem on eraldiseisvaid tellitavaid detaile, mistõttu oleme sunnitud turvalise tellimisaja pikendamisega tarnekindlust tõstma. Eriti hull on olukord, kui pundis on Ettevõte 2 stiilis pakkujad, kelle tarneajad on ebastabiilsed.
Selle kompenseerimiseks tasuks võimalusel tellida stabiilsetelt tarnijatelt rohkem erinevaid komponente. Näiteks kui Ettevõte 1 saab tarnida kaheksast detailist kaks. Tarnekindluse määra peaks küll sellisel juhul pisut kasvatama (0,95^1/2 = 0,975), kuid tema stabiilsust arvestades võib see olla kasulikum, kui neid soetada Ettevõttest 2. Ja seda isegi olukorras, kus soetusmaksumus on Ettevõtte 2 kasuks, kuid laoseisu ja tootmisplaani häiretest tingitud väiksemad kulud on selgelt Ettevõtte 1 eelised.
(Näiteks artikli alguses mainitud ettevõte Power-Packer Europe loobus kalli soetushinna tõttu teatud komponente tellimast kohalikult Hollandi tarnijalt ja hakkas neid ostma odavamalt võõrsilt. Tulemuseks oli tunduvalt pikem tarneaeg, suurem komponentide laoseis ja sagenenud tootmishäired detailide puuduse tõttu.)
Päris elu on muidugi keerulisem, kui siin artiklis arvutuste aluseks olnud sarnaste tarneaegade ja stabiilsustega ettevõtted. Seetõttu tuleks erinevatele materjalidele määrata igaühele oma tarnekindluse määrad ja turvalised tellimisajad.
Näiteks odavatel sisseostetavatel detailidel (näiteks valgusdioodid vms) peaks olema seatud turvaline tellimisaeg väga kõrge tarnekindluse määra alusel, sest nende laos omamine ei ole kuigi kallis.
Kallite komponentide korral (mõni keeruline tehnosõlm vms) tuleks rakendada vastupidi madalat tarnekindluse määra, et hoida suuremast laoseisust tekkinud kulu võimalikult madalana. Mõte peitub selles, et kui materjalide puudusel ei saa tootmisplaaniga jätkata, siis pigem 1000 eurose tehnosõlme kui 25 sendise dioodi tõttu.
Kokkuvõte
Lõpetuseks tasub tarnekindluse osalt meelde jätta peamiselt kaks aspekti. Esiteks see, et fikseeritud tarnekindluse määra juures, kus tarneaegade variatiivsus kasvab, hakkavad suurenema nii turvaline tellimisaeg kui ka laosaldo.
Ja teiseks tuleb arvestada, et mida rohkematelt pakkujatelt materjale tellida, seda suuremad peavad olema individuaalsed tarnekindluse määrad erinevate artiklite lõikes, et tagada üldist õigeaegsuse taset.
Allikad
- 1 M. A. Sieke, R. W. Seifert, U. W. Thonemann, Designing Service Level Contracts for Supply Chain Coordination, Vol. 21, No. 4, July–August 2012, pp. 698–714.
- 2 S. Donderwinkel, Improving the On Time Delivery performance by the implementation of a Sales Inventory & Operations Planning process, Industrial Engineering and Management University of Twente, 2015.