
Oma viis aastat tagasi juhtusin külastama üht Eesti tootmisettevõtet, kus juhid ei olnud rahul tehase läbilaskevõimega ja ka töökäte lisamine ei olnud andnud suurt midagi juurde.
Probleemi lähemalt vaatlema asudes selgusid aga huvitavad käitumismustrid. Töötajad, kes olid oma tööülesande hetkeks lõpetanud, alustasid töövahendeid peitma, kuna lähiajal võis neid uuesti vaja minna ja siis ei pruugi neid käepärast olla. Samal ajal mitmed teised töötajad tegelesid nende „kadunud“ asjade otsimisega.
Sama muster kordus iga päev, kuna vahendeid ei olnud piisavas koguses saadaval. Töötajad arvasid, et ettevõte ei raatsi lisavahendeid muretseda, juhtkond omakorda, kes ise sageli eesliinile ei jõudnud, et kehva produktiivsuse põhjused on pigem töötajate madalas motivatsioonis.
Eelkirjeldatud olukord, kus igapäevaseid probleeme küll lahendatakse, kuid pinnapealselt, ei ole erand, vaid olen neid kohanud ettevõtetes üsna sageli. Eriti eesliinil, kus töötajad puutuvad jooksvate probleemidega vahetult kokku ja neil oleks potentsiaali pakkuda lahendusi, mida juhid ei pruugi märgata.
Järelikult peitub eesliini töötajate probleemilahenduses ühe organisatsiooni tarvis suur arengupotentsiaal, mille edukal kasutamisel oleks võimalik järjepidevalt protsesse täiendada ja sedasi vähendada suure osa korduvate probleemide uuesti esile kerkimist.
Paraku paljud organisatsioonid ei kasuta võimalust arenemiseks eesliinil iga päev esinevate probleemide lahendamise kaudu. Seda isegi olukorras, kus tööd takistavaid probleeme tekib päeva jooksul üsna sageli.
Näiteks USA meditsiinisektoris teostatud uuringud on toonud välja, et ühe eesliini töötaja kohta esines takistusi iga 1,60 tunni tagant. Minu enda aasta tagasi tehtud uuringus ühes Eesti tootmisettevõttes esines tööd takistavaid olukordi isegi sagedamini, lausa iga 1,25 tunni tagant ja selle menetlemine röövis tööajast koguni 17%.

Eesti tootmisettevõttes tehtud uuringust selgus, et eesliinil esines ühe inimese kohta tööd takistavaid olukordi iga 1,25 tunni tagant, millega tegelemine röövis tema kasulikust tööajast 17%.
Miks me ei suuda probleemide lahendamise potentsiaali ära kasutada?
Kuigi probleeme esineb sageli ja kaotame sinna ka märkimisväärselt palju aega, siis organisatsioonid paraku ei ole kuigi head nende lahendamises ning tunnistavad seda endale isegi.
2017. aastal 17 riigis 91 era- ja avaliku sektori organisatsiooni seas läbi viidud uuring näitas, et 85% osalejatest pidas end probleemide lahendamises nõrgaks ning 87% tõi välja, et see on põhjustanud neile märkimisväärseid kulusid.
Järelikult on ettevõtete probleemilahenduse süsteemis tõsine puudujääk, mis eeltoodud uuringu koostajate hinnangul väljendub kalduvuses lülituda “lahenduste režiimi” eelnevalt adumata, kas probleemi tegelikult ka mõistetakse.
Ka mitmed kvaliteediprobleeme käsitlevad uuringud viitavad sarnasele kitsaskohale ja eristavad tasemeti kahte liiki tegutsemismustrit probleemidega tegelemisel: lühiajaline meede (esimese astme probleemilahendus), mille tegutsemisviis on kiirelt “paigata” tekkinud kitsaskoht ning põhjalik lähenemine (teise astme probleemilahendus), mis püüab esmalt uurida, miks kitsaskoht eksisteerib ja lõpptulemusena muuta ettevõttesiseseid rutiine, et vältida probleemi edasist kordumist.
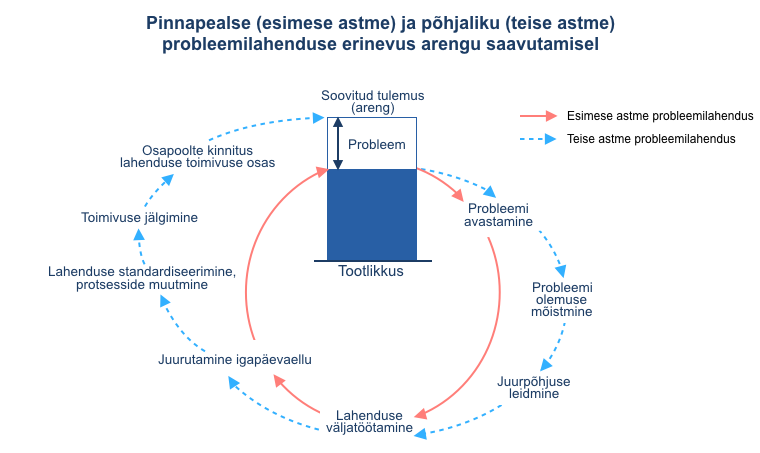
Probleeme tuleb lahendata struktureeritult (teise astme tasemel), siis toimub areng ning nende uuesti esile kerkimine on likvideeritud.
Nii minu tootmisettevõttes teostatud kui ka USA meditsiinisektori uuringud näitasid, et eesliini töötajatel on tugev kalduvus (üheksal juhul kümnest) rakendada esimese astme probleemilahendust, ehk n-ö paikamist, et oma tööga saaks kohe edasi minna.
Selline kiire lahendus ei pruugi aga likvideerida probleemi allikaid (juurpõhjust) ja vastumeede ei ole seega piisav, et tulevikus sarnase probleemi uuesti esinemist vältida. Järelikult avastatakse eesliinil end olukorrast, kus pidevalt küll probleeme „lahendatakse“, kuid need ilmuvad pidevalt tagasi, mis tähendab, et arengut ei ole toimunud.
Esimese hooga võiks arvata, et kalduvus pinnapealseid lahendusi genereerida tuleneb ehk probleemide keerukusest või tööliste alamotiveeritusest. Uuringute käigus teostatud vaatlused näitasid siiski vastupidist.
Probleemid, mida töötajad kohtasid, olid suhteliselt lihtsad ning rutiinsetesse protsessidesse lõimitud. Samuti ei olnud töölised alamotiveeritud ega laisad, sest viibisid sageli kauem tööl või tegid lühemaid lõunapause, kui oli ette nähtud. Järelikult mängivad edukas probleemilahenduses rolli muud tegurid.
Mis takistab eesliinil edukat probleemilahendust?
Tegureid, mis mõjutavad ühe või teise probleemilahenduse mustri kujunemise, toob teaduskirjandus välja palju ja kõiki siinkohal käsitleda ei tarvitse. Küll aga toon välja need, mis omasid suuremat kaalu nii meditsiinivaldkonna kui ka minu enda tehtud uuringus Eesti tootmisettevõttes.
Ollakse koormatud oma põhitööga
Üks määravamaid tegureid, mis takistab eesliinil edukat probleemilahendust, on organisatsiooni isikkoosseisu maksimaalne koormatus oma põhitööga. See on olukord, kus töötajatel pole aega, et diagnoosida ja parandada probleemide juurpõhjuseid.
Töötajad suudavad vaevu ettenähtud aja jooksul oma kohustustega hakkama saada ning on sisuliselt sunnitud probleeme kiiresti paikama, et saaksid tööga edasi minna.
“Ma saan küll probleemide kohta tagasisidet, mida tuleb muuta jne, kuid pole olnud aega nendega tegeleda.”
Kliendihaldur
Selline olukord on omane paljudele tootmisettevõtetele, kus ressursikasutuse huvides seatakse nii masinate kui ka personali võimekus viimasele piirile ning sageli määratakse lausa põhieesmärgiks. Tegemist on ettevõtte personalijuhtimise valikutega.
Kui eesliini töötajatele ei eraldata aega probleemilahenduseks, siis on vaja süsteemi, mis võimaldaks kitsaskohtadest hõlpsasti juhtidele teada anda. Valiku puuduseks on probleemide lahendamise piiratud maht, sest juhtidel ei pruugi samuti aega olla, et kõigi kõrvalekalletega tegeleda.
Teiselt poolt jällegi töötajatele aja eraldamine võimaldab küll paljude probleemidega korraga tegeleda, kuid tähendaks suuremaid personalikulusid või osast tootmismahust loobumist.
Töökeskkond pole psühholoogiliselt turvaline
Tõhusa probleemilahenduse toetamiseks on tarvis organisatsioonis tagada juhtide poolt ka psühholoogiliselt turvaline töökeskkond. See on keskkond, kus töötajad tajuvad, et nende mõtteid ei naeruvääristata ega initsiatiivi karistata ja juhid julgevad tunnistavad ka enda vigu.
Kõike, mida juht räägib või kuidas on minevikus probleeme lahendatud, pannakse töötajate poolt tähele ning sellest tehakse järeldusi. Kui juhi arvates pole mõni teema arutamist väärt, siis hiljem püütakse selliseid diskussioone vältida. See omakorda loob kinnise või avatud suhtluse kliima, mis mõjutab veelgi enam võimet ja valmisolekut tuvastada ja arutada tekkinud probleeme.
“Ma konsulteerin harva müügiosakonna juhtidega, üldjuhul otsustan praagiprobleemide lahendamisel oma kogemuse pealt.”
Operaator
Psühholoogilise turvalisuse õhkkonda kujundab ka see, kui juhid ei soovi, et keegi nende probleemidest teaks, sest neid nähakse nõrkuse ja kehva soorituse märgina. Töötajad võtavad peagi sarnase hoiaku: „see ei juhtunud minu vahetuse ajal“ või „see ei ole meie probleem“.
Mõnel juhul võivad probleemide vältimist ja varjamist tekitada ka organisatsioonilised stiimulid, mis kalduvad üldjuhul premeerima edu ja karistama ebaõnnestumisi. Kvaliteedipreemia loomise näol on stiimuli ebaõnnestumist kogenud ka siinkirjutaja, kus töötajad preemiast kannustades kaldusid probleeme varjama.
Näiteks peideti laos käsitsemisel vigastada saanud tooted pakendis sügavamale. Väljastamisel neid ei avastatud ja kvaliteedipreemia oli töötajatel sellega välja teenitud. Lõppkliendi rahulolu langes. Ettevõttele oleks olnud tunduvalt kasulikum töötajaid julgustada probleeme leidma ja seeläbi tööd parandama.
Pole loodud lihtsat võimalust probleemidest teada anda
Psühholoogiliselt turvalisele keskkonnale lisaks on tarvis ka lihtsat ja mugavat võimalust tagasiside andmiseks. Ideaalis võiks see toimuda kohe, kui probleemi juurpõhjus on veel kättesaadav.
Probleemile reageerimise kiiruse olulisusele viitab ka MacDuffie oma uuringus, kus võrreldi kolme autotootja meetodeid kvaliteediprobleemide lahendamisel ning tõsteti esile Honda tehast, kus rutiin nägi ette probleemi vahetut väisamist selle tekkimiskohas.
Toyota Californias asuvas NUMMI tehases on probleemidele kiireks reageeringuks antud töötajatel lausa õigus käivitada teavitussignaal (andon-signaal), mis seiskab vajadusel tootmisliini, et kohe tekkinud takistus kõrvaldada. Samas ei ole tegemist teguriga, mida saab määratleda vaid kiiruse kaudu.
Mõned tootmisettevõtted on organisatsiooni reageerimisvõime parandamiseks loonud spetsiaalsed üritused, kus probleemi lahendajad esitlevad oma tulemusi tavatöötundide ajal ettevõtte kohvikus. Tehase juht võtab endale moderaatori rolli, kus jagab tunnustust ja kommentaare iga esitluse kohta.
“…aegajalt läheb 4-5 tootmiskorda, enne kui üldse midagi muutub.”
Operaator
Järelikult, lisaks kiirusele peab organisatsioon olema võimeline probleemilahenduse initsiatiividega tutvuma ja vajadusel hõlbustama vastutusvaldkondade üleseid parendusi, mis aitavad kokkuvõttes vähendada probleemide esinemise sagedust.
Probleemilahenduse metarutiini puudumine
Teise astme probleemilahenduse rakendamist võivad takistada ka selleks tarbeks loomata jäänud formaalsed protseduurid ehk metarutiinid.
Metarutiinid on standardiseeritud probleemilahenduse protseduurid olemasolevate töörutiinide täiustamiseks või uute loomiseks. Töörutiinid omakorda on ennustatavad tegevusmustrid (standardid), mida kasutatakse organisatsioonis tööülesannete teostamiseks.
“Probleemide lahendamiseks küll meil mingit ettekirjutatud asja ei ole, igaüks lahendab nii nagu ta oskab seda lahendada, kuna kõigil on hullult kiire, siis mingi metodoloogia kasutamine tunduks võib-olla ajaraiskamisena. Lihtsam on võtta üks telefonikõne ja see kuidagi kaelast ära saada, kuid tegelikult asi ei lahene…”
Planeerija
Näiteks Toyota Motor Corporationit on saatnud pikaajaline edu, kuna viimane on parandanud pidevalt oma olemasolevaid töörutiine, kus probleemilahenduse metarutiinil on olnud ettevõtte arengus oluline roll.
Toyota autotehased kasutavad protsesside arendamise metarutiinina struktureeritud probleemilahenduse metodoloogiat A3. See on üheleheline aruanne, mis põhineb oma ülesehitusega PDCA (plan-do-check-act)-mudelil.
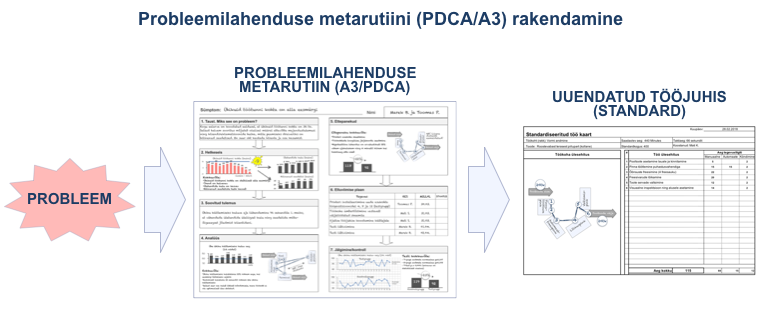
Metarutiini ülesanne on probleeme lahendada struktureeritult (teise astme tasemel) ning seejärel viia toimiv lahendus sisse tööjuhisesse (standardisse), et saavutada tööprotsessis areng.
Oma uuringus tuvastasid Gosh ja Sobek, et kui metarutiini (A3-aruande 9-etapilist struktuuri) järgiti täiel määral, siis tõi see kaasa protsessi 77%-100% arenguefekti. Samas need juhtumid, kus analüüsi tehti poolikult, tunnistasid mõnevõrra väiksemat sooritusefekti – 17%-60%.
Tootmisväljundit peetakse korduvatest probleemidest tähtsamaks
Olgugi, et metarutiini kasutamisel on muljetavaldav mõju lahenduse tõhususele, siis ettevõtete igapäevaellu selle rakendamine mingitel põhjustel takerdub. Üheks võimalikuks põhjuseks võib lugeda juhtide seatud survet tootmisväljundile.
Näiteks eksimuste korral on olulisem vigade parandus, kuna ajaline investeering probleemide lahendamisse tooks kasu alles mõne aja pärast (ja seegi ei oleks kindel).
“Praegu on meil pigem vigade parandamisel fookus, sest ma näen, et ei ole aega analüüsi teha ja jooksvalt parandusi sisse viia ja töötajad on ka seetõttu usu kaotanud ning kuulnud tihti, kuidas öeldakse, et mis neid vigu ikka kommenteerida, nagunii midagi ei muudeta.”
Planeerija
Seevastu defektsete toodete ümber- või uuesti tegemine annaks kohe käegakatsutava tulemuse, seda enam et materjalidesse ja tööjõudu on uputatud märkimisväärne hulk ettevõtte rahalisi vahendeid.
Kokkuvõtteks
Isegi kõige edukamates ettevõtetes esineb probleeme ja eesliini töötajad seal puutuvad paljudega neist vahetult kokku. Need takistuste või eksimustena esinevad olukorrad on suurepäraseks võimaluseks protsesse või protseduure paremaks muuta, kui probleemid õigel hetkel avastada ja seejärel lahendada.
Ometigi näitavad erinevad uuringud, et organisatsioonid ei pruugi olla võimelised eesliinil iga päev esile tulevaid probleeme tõhusalt lahendama ja nõnda tegelikku potentsiaali arenguks ära kasutama. Isegi siis, kui tehase digitaliseerimisega on probleemid oluliselt nähtavamaks muutunud.
Potentsiaali rakendamise asemel eelistatakse viimse piirini disainitud organisatsioonistruktuuri, kus peale peamise tööülesande täitmise muuks aega ei jää. Samuti peetakse olulisemaks tegeleda juba juhtunud eksimuste likvideerimisega kui vigu tekitanud olukordade analüüsimisega.
Kui lisaks eelnevale peetakse probleeme nõrkuse märgiks ja neid ei taheta endale tunnistada ning puudub ka organisatsiooniülene probleemilahenduse protsess (metarutiin), siis on saavutatud täiuslik pideva tule kustutamise töökeskkond, kus probleeme küll lahendatakse, kuid need tulevad uuesti ja uuesti tagasi.
Refereeritud allikas:
- Bankiir, M. (2019). Probleemilahenduse mustrid tootmisettevõtte operatiivtasandil. Tartu Ülikool.