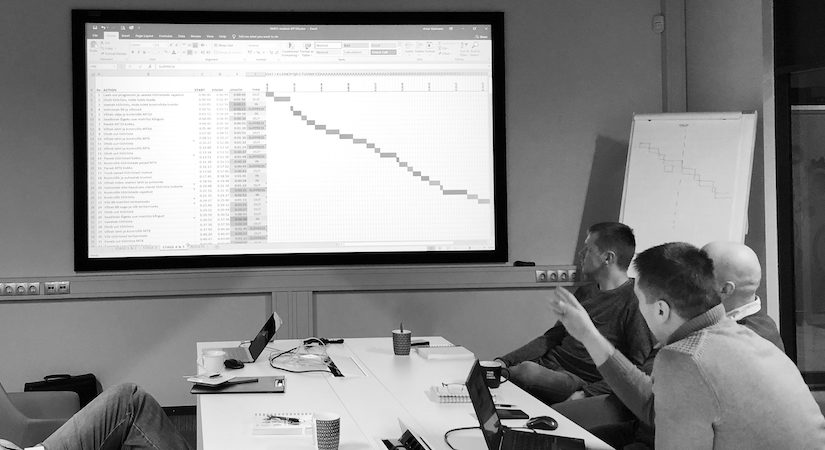
Üks omamoodi dilemma, millega tootmisprotsesside optimeerijad kokku puutuvad, on tootevahetuste optimeerimisest saadava kasu rakendamine. Elu näitab, et pea alati minnakse käegakatsutava kasu lõksu.
Aga alustame esmalt ABC-st.
Tootevahetus ehk masinate seadistamine ühelt tootelt teisele üleminekuks, on üks suuremaid ajakulu komponente, mis röövivad seadmete väärtuslikku ressurssi. Järelikult kannatab ajakao tõttu ettevõtte seadmetesse tehtud investeeringute tasuvus.
Mida siis ette võtta?
Kuna tootevahetuste puhul on tegu planeeritud tööaja ühe suurima raiskajaga, siis selle kompenseerimiseks näevad paljud ettevõtted lahenduseks suuri tootmispartiisid. Üldjuhul selgitatakse seda endale lihtsa loogikaga.
Mida rohkem ühikuid ühe formaadiga toota, seda harvem peab tootevahetusi tegema ja nii tuleb ühtlasi ka ajakulu ühe detaili kohta väiksem (vaata tabelit all).

Traditsiooniliselt kompenseeritakse tootevahetuse aega partii suurusega, sest mida suurem on partii, seda väiksem on ajakulu ühe detaili kohta.
Lean-tootmise loogika aga ei armasta suuri partiisid, sest need on raiskamiste allikaks (ületootmine, varud, transport jm) ning kaotab ära paindlikkuse kliendinõudlusele reageerimisel. Seega on vaja tootevahetused saada nii kiireks kui võimalik.
Kiire tootevahetuse tehnika ehk SMED
Tootevahetuste kiiremaks tegemisel on lean-juhtimise tööriistakotis oma tehnika – SMED. Minemata siinkohal võtte rakendamise peentesse nüanssidesse, on võimalik sellega vähendada minimaalsete rahaliste kulutustega tootevahetustele minevat aega märkimisväärselt.
Eesmärgiks on saada tootevahetuste aeg alla 10 minuti¹. Alati ei ole see küll võimalik, kuid väiksem ülemineku aeg annab suurepärase võimaluse võtta kasutusele väiksemad partiid, ilma et ajakulu ühiku kohta oluliselt kannataks (vaata tabelit all).

SMED-i rakendamisel saavutatud kiirem tootevahetuse aeg kaotab ära suure partii eelise
Kuigi lean-juhtimine näeb ette tootevahetuste lühendamisest saadud efekti rakendamise lühemate partiide kasuks, siis paraku näitab kogemus erinevate ettevõtetega, et valdkonna juhid otsustavad pigem profiiti lõigata suurenenud võimekuse arvelt.
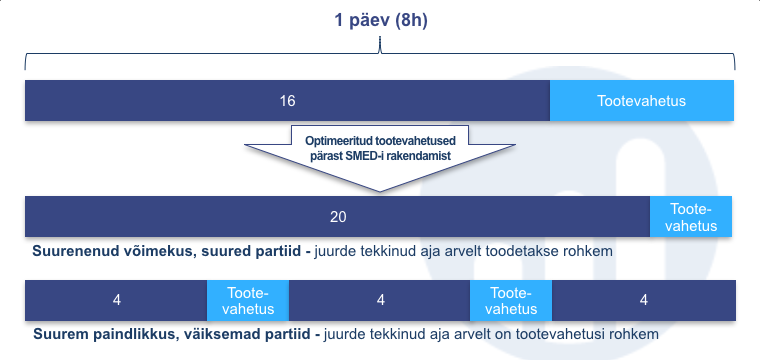
Tootevahetuse lühenemisest on võimalik rakendada kahel viisil: kasvatada võimekust või suurendada paindlikkust.
Põhjus on üsna lihtne, inimesed mõtlevad lineaarselt ja palju käegakatsutavam on mõista kasu suurenenud võimekusest kui sellest, mida annaks omakorda sagedasemad tootevaahetused. Kui ühel juhul on 1+1=2, siis teisel juhul on vastuseks umbmääraselt deklareeritud kasud nagu vähem raiskamist või rohkem paindlikkust jne.
Võimekuse kasuks otsustamine oleks siiski libe tee ja kohe selgitan miks.
Suurte partiide nähtamatu nuhtlus
Nagu eelnevalt toodud, siis tootevahetuse efekti armastatakse rakendada võimekuse suurendamisse, mis omakorda tähendab ka suuremaid tootepartiisid. Need omakorda toovad välja protsesside nähtamatu nuhtluse – variatsiooni.
Just, suurem partii tähendab protsessis ka suuremat variatsiooni. Ja see tekib partiipõhisel tootmisel nende saabumisel töökeskustesse. Võtame ühe lihtsa näite. Oletame, et tõstukijuht toob iga vahetuse alguses (8h) töökeskusesse 20 pooltoodet. Võiks ju arvata, et kui iga päev nõnda materjalid töökeskusesse tuuakse, et siis on variatsioon 0. Päris nii see siiski ei ole.
Hoopis teistsuguseks muutub pilt, kui hakkame partii saabumist töökeskusesse jälgima ühe ühiku lõikes. Saabumistevaheline aeg esimese ühiku kohta on 8 tundi. Kõigi järgneva 19 pooltoote saabumisaeg on 0. Järelikult keskmine saabumistevaheline aeg on 0,4 tundi (8/20=0,4), dispersioon 3,04 ja variatsioonikoefitsent ruudus seega 19 (lihtsamal kujul arvutatuna: partii suurus – 1).
Võttes appi Little’i ja Kingmani seadused (ja valemid), saame kujundada lihtsa mudeli (andmed toodud kokkuvõtvalt alloleval joonisel) partii suurusest tingitud variatsiooni mõjust läbimisajale.
Võttes eelduseks, et tootmisplaneerija suudab töökeskust koormata 50% ulatuses (tegelikult sõltub see samuti partii suurusest, kuid lihtsuse huvides jätame selle muutuja praegu välja), siis väiksema partii (4 tk) korral on ühe menetletava tüki suhe läbimisaega üle kolme korra väiksem kui suurema partii korral (20 tk). Oluline erinevus, kui kliendi perspektiivi silmas pidada.
Aga mis juhtus läbilaskevõimega? Meid ju huvitas, kumb on kasulikum, kas juurdesaadud tootmismaht või väiksemate partiide nähtamatu efekt. Jällegi kasutame selle selgitamiseks Little’i seadust järgnevalt.
Nagu selgub, siis väiksemad partiid on kasulikumad isegi tootmisvõimekuse aspekti silmas pidades², kuigi tootevahetuse efekti dilemma partiide suurendamise suunas võib näiliselt nii mõnelegi tootmisjuhile ahvatlev olla.
Mis sellest kõigest järeldada? Eelkõige ehk seda, et tootmise operatsioonisüsteem ei ole keskkond, kus saaksime lineaarse mõtlemisega otsuseid teha, sest variatsioon oma destruktiivse olemusega on üks tõeline nuhtlus.
¹ SMED on inglisekeelne akronüüm “single minute exchange of dies“, mis otsetõlkes võiks tähendada “ühe minutiga stantside vahetamine”. Samas erialakirjandus toob välja, et SMED-i autor Shigeo Shingo pidas “single minute” termini asemel silmas “single digit’t” ehk “ühekohaline number”, mis ühtlasi tähendabki tootevahetuste viimist alla 10 minuti.
² Siinkohal on tegu siiski üldistusega. Partii optimaalne suurus (läbimisaja aspekti silmas pidades) sõltub siiski tootevahetuse ajalisest pikkusest. On olukordi, kus väike tootmispartii on ettevõttele pigem kahjulik. Loe täpsemalt siit: Lean-tootmise ebarealistlikud eesmärgid.